Application of H7-1200 PLC in Thermal Oil Furnace
2024-04-17
Huceen
Environmental standards and regulations have increasingly strict restrictions on the use of newly started coal-fired thermal oil furnaces. Environmental policies and laws require the elimination of existing coal-fired thermal oil furnaces that pollute the environment, and the promotion of cleaner combustion of natural gas thermal oil furnaces and biomass energy thermal oil furnaces, thereby reducing pollutant emissions, continuously purifying the environment, and promoting sustainable economic and social development.
The operation modes of fully automatic burners for burning natural gas include single stage, two-stage, two-stage progressive, and proportional adjustment. Under the same conditions, proportional adjustment should be given priority.
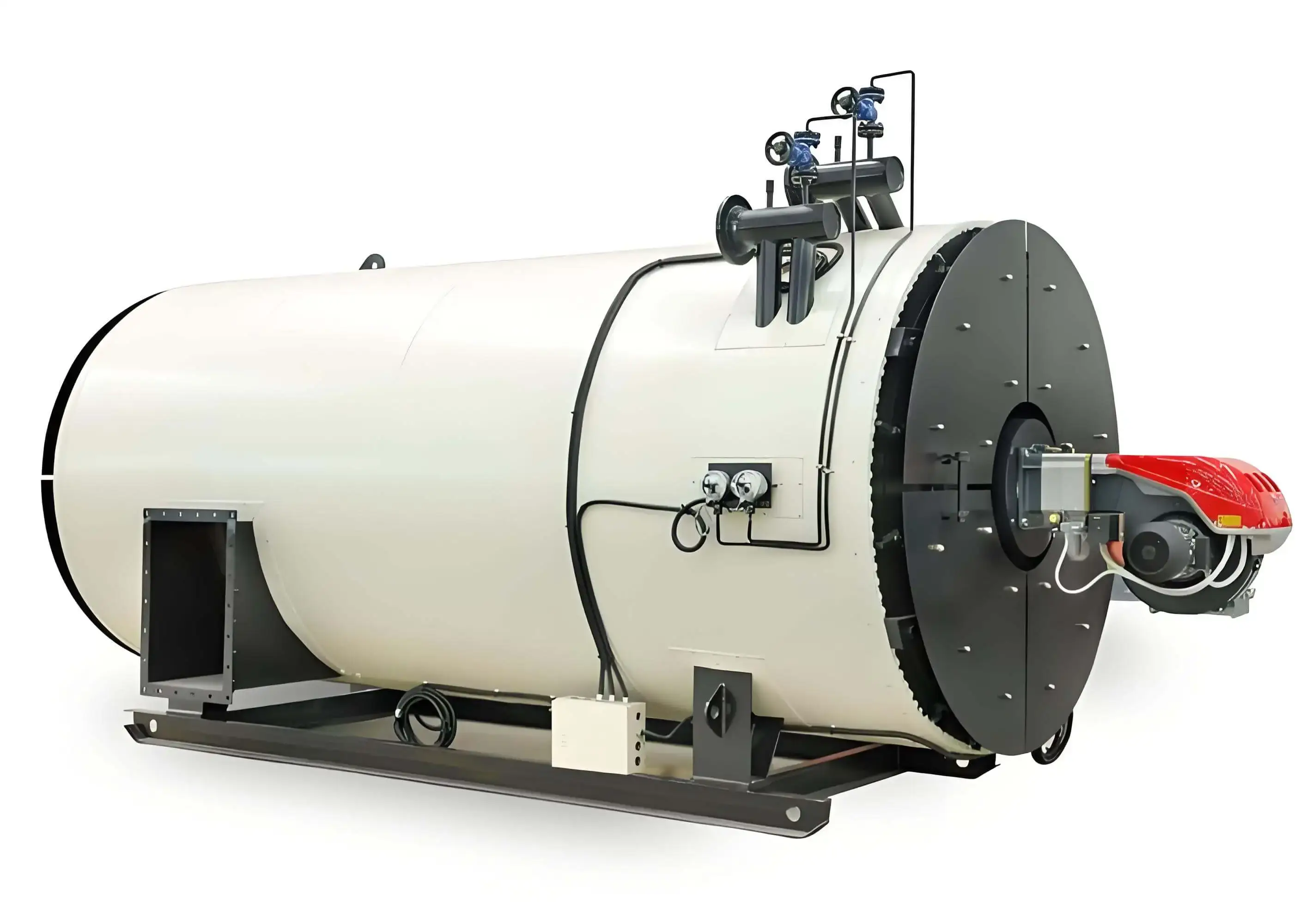
Project Introduction
The structural design of natural gas thermal oil furnaces usually adopts a circular coil structure. The reason is that the circular coil structure is arranged compactly, and its cylindrical combustion chamber is very suitable for the shape of natural gas flames. Moreover, the thermal oil flows in the heating surface without any dead corners, and is uniformly heated.
The natural gas thermal oil furnace is composed of several parts, including a natural gas burner, furnace body, smoke box, insulation layer, inner and outer cylindrical steel protective plate, tail flue gas waste heat recovery device, support base, etc. The furnace body adopts a circular coil structure, and the coil bundle component is composed of two concentric combinations of inner, middle, and outer coils. The cylindrical space enclosed by the inner coil is the combustion chamber. After natural gas fuel is burned in the combustion chamber and radiated to release heat, high-temperature flue gas enters the flue gas channel between the inner coil and the middle coil, as well as between the middle coil and the outer coil. After two rounds of convective heat exchange, the flue gas enters the tail flue gas waste heat recovery device from the rear of the furnace and is directed to the chimney.
PLC control system configuration
The main control system uses SIMATIC S7-1200 CPU, combined with the extended Huceen H7-1200 series analog input module to collect temperature (such as oil outlet temperature, return oil temperature, exhaust gas temperature, etc.), pressure (oil outlet pressure, return oil pressure, expansion tank pressure, oil storage tank pressure, etc.), frequency, opening, flow rate and other data. The Huceen H7-1200 series analog output module is also used for frequency control, opening control, combustion engine fire setting, etc.
PLC configuration table | |||
Number | name | model | notes |
1 | CPU | 6ES7 214 1BG40 0XB0 | 1214C AC/DC/RLY |
2 | Analog module | H7 231-4HF32-0XB0 | AI8 |
3 | Analog module | H7 232-4HD32-0XB0 | AQ4 |
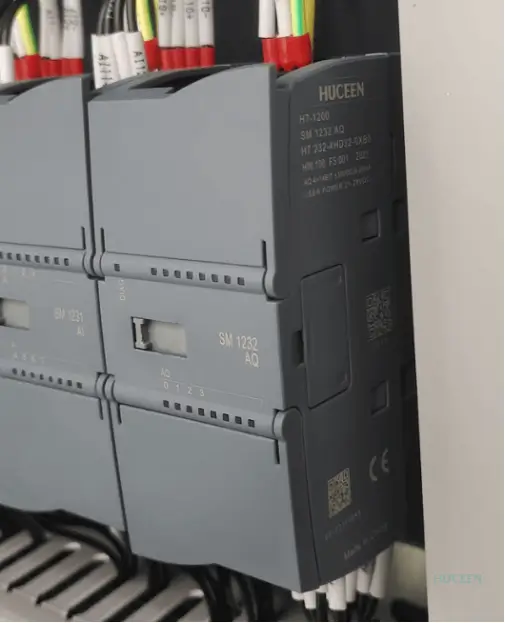
Major function
Automatic control is carried out in accordance with the combustion safety operation regulations and ignition and combustion procedures of the thermal oil furnace to ensure safe, reliable, and economical operation of the thermal oil furnace. After successful ignition, a timely ignition success signal is sent to the control system. At the same time, the flame detection device always detects the combustion situation of the small flame, maintaining its long open flame. When burning normally, once the natural gas burner flame is found to be extinguished, the corresponding flame detector will quickly detect it and send an extinguishing signal to the PLC for monitoring and control. When the natural gas combustion system suddenly goes out, quickly cut off the natural gas pipeline valves from the small and large fires in the combustion system to avoid the occurrence of explosion accidents.
The outlet temperature of the natural gas thermal oil furnace has an automatic adjustment function. This regulation system is based on the data corresponding to the requirements for the outlet temperature of the heat transfer oil furnace as the given value for adjusting the heat transfer oil temperature. Then, it is compared with the actual heat transfer oil temperature at the outlet of the heat transfer oil, and the comparison error is PID calculated. Taking into account various factors, feedforward control, cascade control, etc. are used to control the natural gas flow control valve, regulate the natural gas flow rate, and adjust the air volume according to the proportion of natural gas flow rate while adjusting the natural gas flow rate, ensuring the proportion of air and natural gas, thus achieving the purpose of regulating the outlet temperature of the heat transfer oil furnace.
When selecting the automatic operation mode for the combustion natural gas thermal oil furnace automatic control system, press the automatic start button to first start the circulating thermal oil pump. After normal operation, the fan will blow it. After the blowing time is up, the PLC will send the ignition command of the ignition system according to the control requirements, and detect the working condition of the burner online. When the requirements are met or everything is normal, control various parameters according to the predetermined program. During startup and normal operation, timely check the condition of various equipment and detection points in the system, and issue corresponding control commands and sound and light alarm signals when abnormal situations or faults are found.
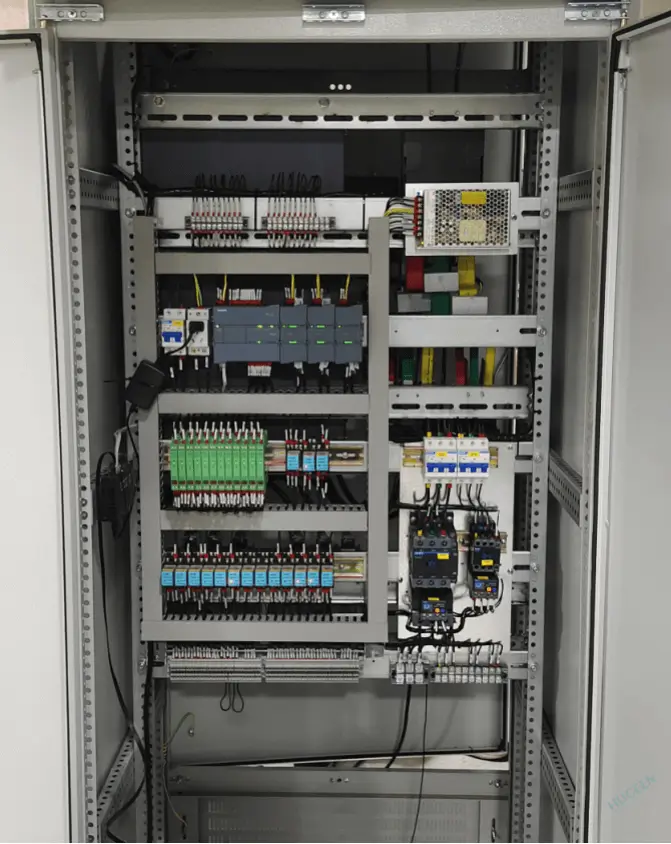